In today’s fast-paced manufacturing environment, efficiency and adaptability are critical for businesses striving to stay competitive. Among the various manufacturing techniques, injection moulding stands out as one of the most versatile methods for producing high-quality plastic components. To fully leverage the advantages of this process, collaborating with a reliable injection moulding machine supplier is essential. Such partnerships offer numerous benefits, including customisation of machines, flexibility in production, and vital technical support that enhances overall operational efficiency.
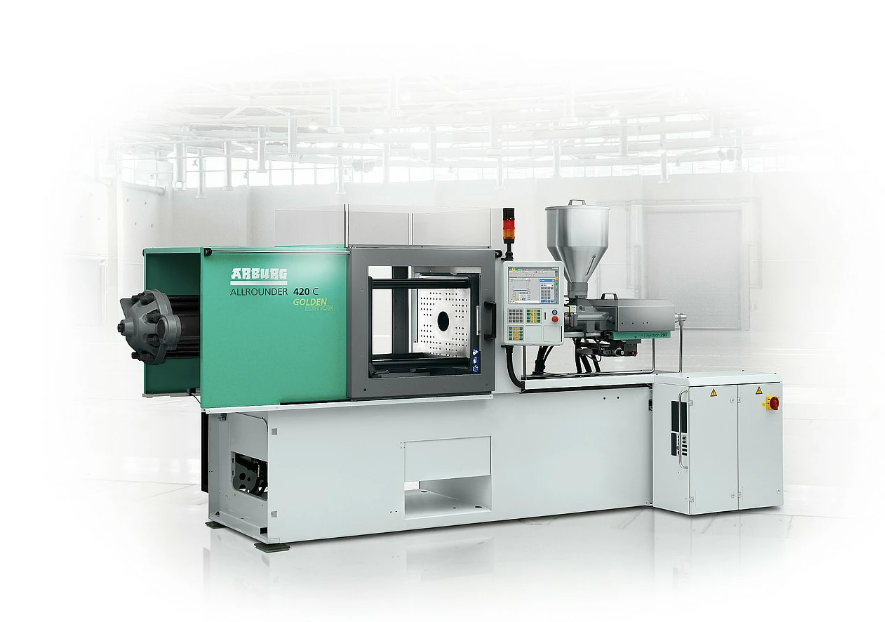
Content
The Importance of Customisation in Injection Moulding
One of the primary advantages of working with a machine supplier is the opportunity for customisation. Every business has unique requirements based on its specific products and production goals. Off-the-shelf machinery may not always meet these needs, leading to inefficiencies and potential production delays. A supplier that understands the nuances of your operations can design and modify equipment to ensure that it aligns perfectly with your manufacturing process.
Customisation can encompass various aspects, such as the size and shape of the moulds, the type of materials used, and the overall machinery specifications. By offering bespoke solutions, a supplier allows businesses to create products that meet exacting standards and specifications. This tailored approach not only improves product quality but also maximises production efficiency, ultimately enhancing a company’s competitiveness in the market.
Furthermore, customisation enables manufacturers to respond swiftly to changing market demands. When businesses can adapt their production processes to accommodate new designs or materials, they can seize opportunities that arise from shifts in consumer preferences or emerging market trends. This agility is a significant advantage in an increasingly dynamic business landscape.
Flexibility in Production Processes
In addition to customisation, flexibility is another critical benefit of collaborating with an injection moulding machine supplier. The ability to adjust production volumes, change product designs, or switch between different materials is essential for manufacturers aiming to maintain a competitive edge. An experienced supplier understands the challenges associated with production variability and can provide machinery that accommodates these needs.
For instance, during periods of high demand, businesses may need to scale up production quickly. An injection moulding machine supplier can offer solutions that facilitate this transition, such as machines designed for rapid production or the integration of additional moulds that allow for concurrent production runs. This flexibility ensures that companies can meet customer demands without compromising on quality or efficiency.
Moreover, as businesses grow and evolve, their production needs may change. Working with a supplier that offers modular or upgradeable machinery allows manufacturers to adapt to these changes without significant financial investment. This scalability is particularly important in industries characterised by rapid technological advancements or shifting consumer preferences, as it enables manufacturers to remain relevant and competitive.
Technical Support: A Pillar of Success
Technical support is a fundamental aspect of any partnership with an injection moulding machine supplier. The complexities of injection moulding machinery require specialised knowledge to operate and maintain effectively. A reliable supplier not only provides the machinery but also offers ongoing support that ensures optimal performance throughout the equipment’s lifecycle.
Initial training on the operation and maintenance of the machinery is crucial for manufacturers to get started on the right foot. A supplier typically provides comprehensive training sessions, equipping staff with the necessary skills to operate the machines safely and efficiently. This training helps to minimise the risk of operational errors, which can lead to production downtime and increased costs.
Furthermore, technical support extends beyond initial training. As production processes evolve, manufacturers may encounter challenges that require expert assistance. A dedicated supplier offers continuous support, helping businesses troubleshoot issues, optimise machine performance, and implement maintenance strategies that prolong equipment life. This ongoing relationship ensures that manufacturers can rely on their equipment to perform consistently, reducing the risk of unexpected breakdowns that could disrupt operations.
Enhancing Product Quality and Consistency
Another critical advantage of partnering with an injection moulding machine supplier is the enhancement of product quality and consistency. High-quality machinery designed and maintained by experienced suppliers significantly impacts the final products. Advanced technologies incorporated into modern injection moulding machines, such as precise temperature control, improved mould design, and enhanced automation, contribute to producing parts with minimal defects.
When businesses work closely with their suppliers, they can benefit from the latest advancements in injection moulding technology. Suppliers are often at the forefront of innovation and can provide insights into new techniques and materials that can improve product quality. By implementing these advancements, manufacturers can achieve higher levels of accuracy and consistency, leading to reduced waste and increased customer satisfaction.
Additionally, suppliers can assist in conducting quality assurance checks and implementing best practices for production processes. This collaboration ensures that manufacturers adhere to industry standards and maintain a reputation for producing reliable and high-quality products.
Cost Efficiency Through Strategic Partnerships
While the initial investment in custom machinery may seem significant, working with a reputable injection moulding machine supplier often leads to long-term cost savings. The efficiency gained from customised solutions, flexibility in production, and ongoing technical support ultimately results in reduced operational costs.
By investing in machinery tailored to specific production needs, manufacturers can optimise their workflows, minimise material waste, and reduce energy consumption. This efficiency translates into lower production costs, allowing businesses to allocate resources more effectively and improve profitability.
Moreover, a strategic partnership with a supplier fosters collaboration on cost-reduction strategies. Suppliers can offer insights into bulk purchasing agreements for materials, streamlined processes, and technological advancements that lead to cost savings. This collaborative approach positions businesses to remain competitive in a challenging market while maintaining healthy profit margins.
Conclusion:
In the realm of manufacturing, the importance of choosing the right partners cannot be overstated. Collaborating with an experienced injection moulding machine supplieroffers a multitude of benefits that extend beyond the machinery itself. From customisation and flexibility to invaluable technical support and enhanced product quality, the advantages of such partnerships are profound.
As businesses navigate the complexities of modern manufacturing, the need for adaptability, efficiency, and expertise becomes increasingly apparent. By investing in a relationship with a reliable injection moulding machine supplier, manufacturers position themselves for success, ensuring they can meet market demands while maintaining high standards of quality and performance. This partnership is not merely a transactional arrangement; it is a strategic alliance that can significantly influence a company’s trajectory in an ever-evolving industry landscape.
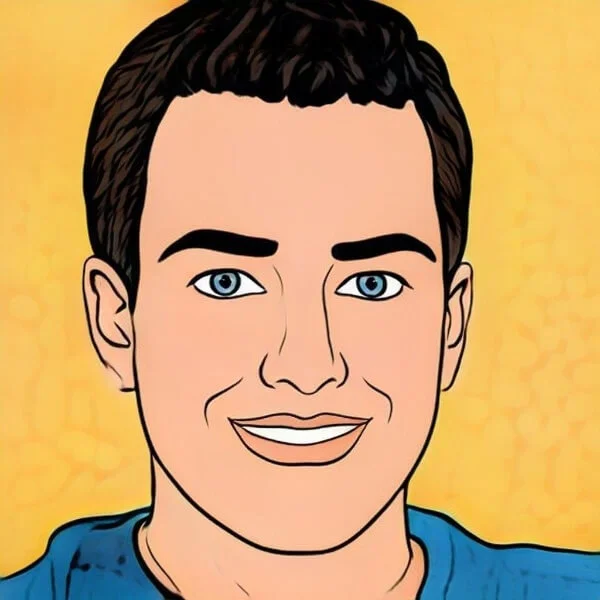
Joey is your friendly neighborhood knowledge seeker. From science to history, he’s on a quest to unravel the mysteries of the universe and share his discoveries with you. Dive into his articles for a dose of curiosity and wonder.